TSUBAMEX's Strengths
Connected Systems with a 3D Design System and Production Management System as the Core
TSUBAMEX's 3D design system has been cultivated in the die manufacturing field with a focus on efficiency and connectivity. It connects factories seamlessly and achieves smooth progress and management.
3D Design System
Strengths in digital transformation and die manufacturing that start with a 3D design system
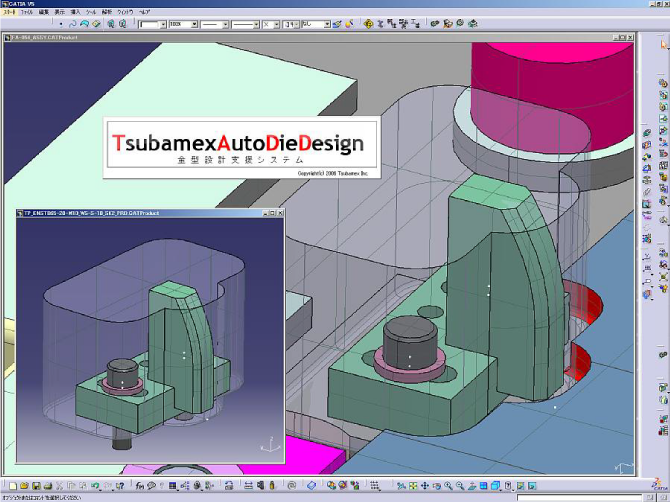
Efforts to shorten lead times began in 1982 with the introduction of CAD/CAM systems, and continued to be developed with our original TADD system as the core.
It starts with automation of the design area, which is the core of manufacturing, and links to the management and sharing of sales information, bill of materials information, performance information, and cost information. It has evolved into an environment where all information can be viewed by anyone, anytime, anywhere.
Shortening lead times is one objective for "letting systems do what they can do, and letting people take on creative work." The TADD system has shortened lead times and will be developed into a next-generation system under more flexible cooperation.
[Generation 1]
2D TADD
(Tsubamex Auto Die Design system)
<1983-1990>
![[Generation 1]](../assets/images/feature/img2.png)
Introducing CATIA/CADAM for the first time as a Japanese company; 2D TADD aimed for automatic design.
In an age where automotive manufacturers developed CAD/CAM systems internally, we introduced commercial CAD/CAM systems and established NC processing technology. That initiative was widely known as the first case in the die industry, with accepting many factory visitors at Tsubamex as a result.
CATIA, which we introduced in 1982, became the origin of the 3D TADD system. Following this, CADAM in 1983 was the source of automatic design.
Commercial CAD/CAM systems are versatile, but not specialized for specific corporate business (or culture).
TSUBAMEX successfully developed systems specialized for die manufacturing to enhance competitiveness and the speed of design.
One of the systems is automatic drawing generation system which creates drawings based on 3D data.
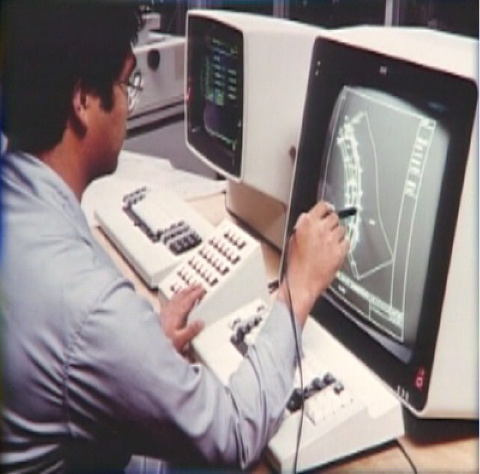
[Generation 2]
3D TADD
<1990-1998>
![[Generation 2]](../assets/images/feature/img4.png)
Making 3D solid design a reality.
Visualizing performance, schedules, and costs.
On the basis of our know-how regarding 2D TADD, we developed TSUBAMEX's own 3D solid design that uses CATIA systems in 1998.
By making use of the automatic drawing generation system, all designers were able to start 3D solid design.
We developed two systems in parallel.
We built a bill of materials system and a die management system—both of these served as a foundation for the production management system.
A performance collection system, which digitized handwritten daily reports, is linked to IoT systems.

[Generation 3]
Expansion and Improvement of 3D TADD
<1999-2004>
![[Generation 3]](../assets/images/feature/img6.png)
Creating a viewer system that utilizes an online environment, and making forming simulation a reality through joint development. The third generation was the age of expansion and improvement for an open and connected environment.
In the early 2000s, the systems we built in the second generation were linked with data and information.
Design data was connected to an order-receiving and -placement system, and CAD information was provided to workshops through a portal site and viewer system.
These systems began to be linked to customers on a large scale.
Based on the CAD/CAM knowledge we cultivated from the 1980s, we conducted joint development with research institutes and universities.
This resulted in the realization of forming simulations and ultra-high-speed processing machines.
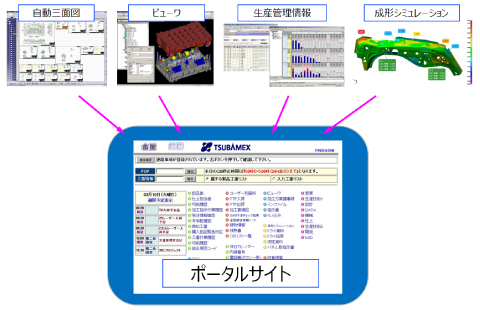
[Generation 4]
3D TADD + TCS
<2008-2020>
![[Generation 4]](../assets/images/feature/img8.png)
![[Generation 4]](../assets/images/feature/sp-img8.png)
Expanding manufacturing networks through flexible connections.
TCommencement of the Tsubamex Connected System (TCS) with TADD as its core.
We integrated various platforms into Windows (CATIA V5), and established an environment for reviewing designs through a viewer. Through this, connections between systems were reinforced.
We built the "TSUBAMEX Network", a cooperative platform that allows anyone to access the latest information anytime, anywhere.
We began to deploy this platform, which can be accessed from both PC and tablet, to partner companies.
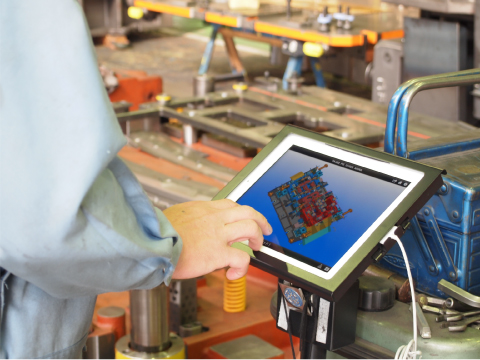
Production Management System
Strengths in metal processing (mass production) and digital transformation of production management systems
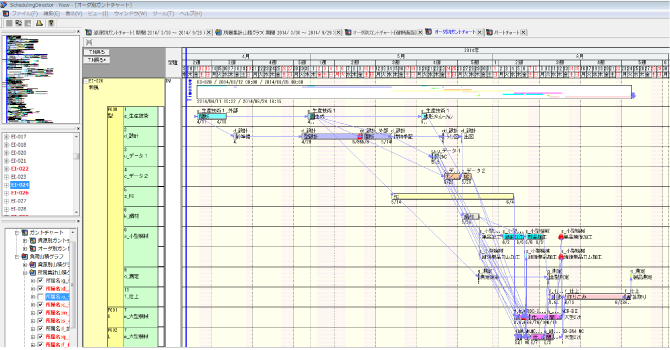
Metal processing (mass production) began in 1892 started in producing File, a shaver for metal, which has been developed into metal presswork technology for stainless steel and plastic molding technology.
We have technology and equipment for all kinds of processing, including single-shot and progressive press processing methods, insert forming technology connected with forming technology, and press processing starting from 0.1-mm to deep drawing processing that goes tens of centimeters deep.
Our production management system for metal processing and mass production, which is based on our production management system for die manufacturing, automatically collects the performance of processing equipment by using IoT devices and achieves accurate production planning and high productivity.
Production Management and Backbone
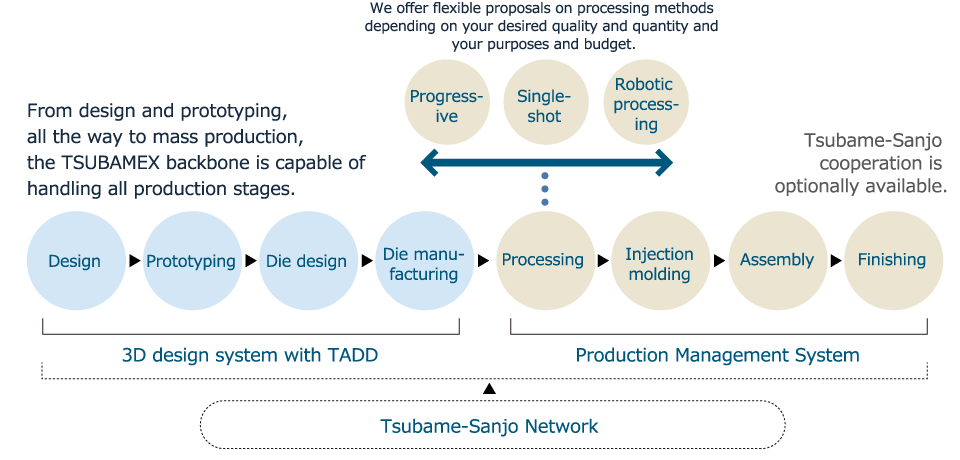
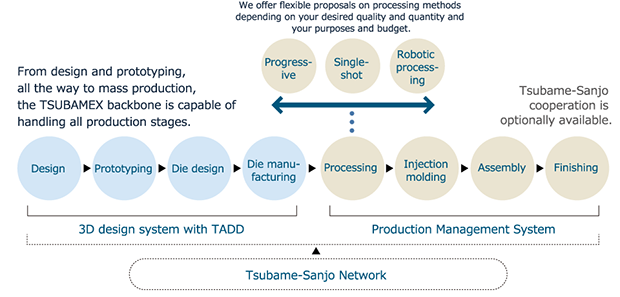
The Tsubamex Connected System (TCS) has made one-stop manufacturer functions a reality